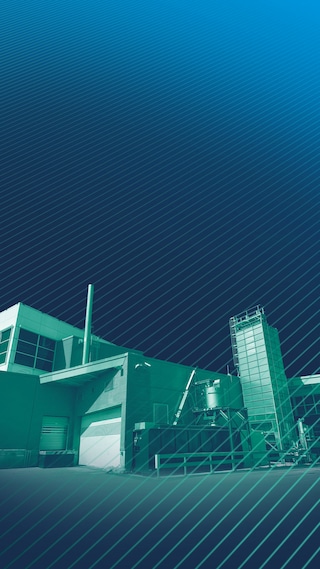
How do you make a
carbon-neutral factory?
Explore Philip Morris International’s journey
toward climate-neutral thinking through the
prism of one factory’s transformation.
How do you make a
carbon-neutral factory?
Explore Philip Morris International’s journey toward climate-neutral thinking through the prism of one factory’s transformation.
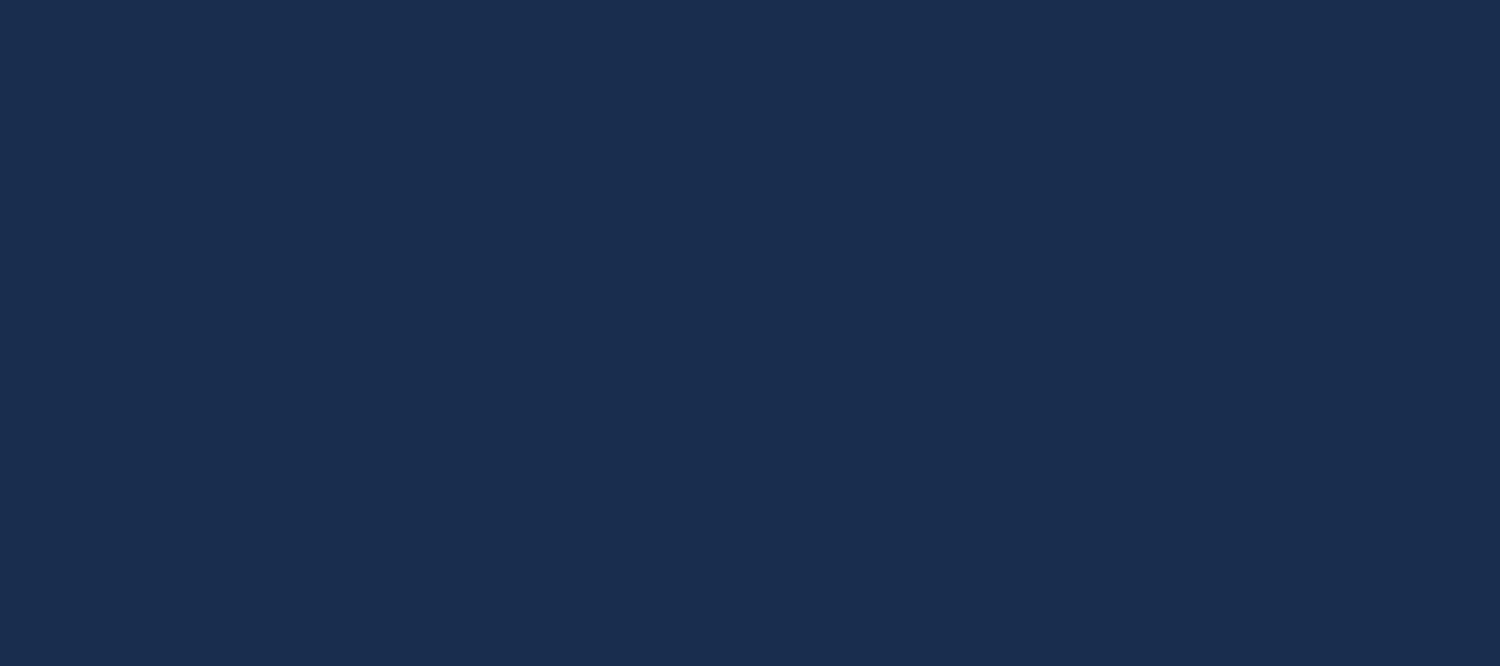
Why is PMI targeting carbon-neutrality?
As a business with a multinational environmental footprint, Philip Morris International (PMI) will continue to play a role in contributing to addressing the climate crisis. We are achieving this by reducing our emissions of carbon dioxide—the main greenhouse gas driving climate change—to advance our transition toward a “climate-neutral” economic model.
Our carbon-neutrality work covers our entire value chain, from the “upstream” supply of tobacco and other materials (around 85 percent of our CO2 emissions) to the “direct operations” of production, packaging, and commercialization (around 10 percent), and finally the “downstream” use and end-of-life of our products (around 5 percent).
The greatest impact can be found in our upstream operations, and we’re already making significant progress in this area. But PMI is also committed to reducing emissions in its direct operations, by transitioning to green and renewable energy.
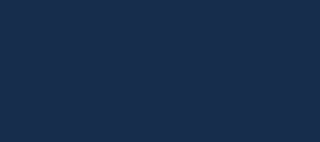
This is one of the many solutions PMI applies to its direct operations to reduce consumption and optimize energy efficiency while minimizing the use of fossil fuels and promoting the switch to renewable energy.
One example of this is our factory in Neuchâtel, Switzerland, which became carbon-neutral in 2021.
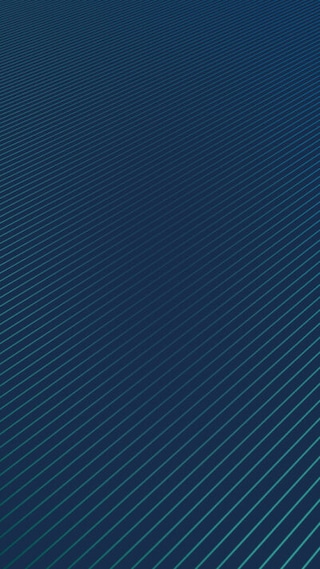
How does the Neuchâtel factory work?
How does the Neuchâtel factory work?
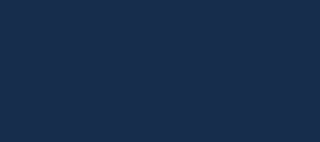
PMI’s factory in Neuchâtel, Switzerland, has begun using pyrolysis technology, which converts organic waste produced in the factory—including carton, wood, and tobacco leaves—into green energy.
The factory utilizes its location beside Lake Neuchâtel by using cold lake water to cool the machinery and buildings. As a result of this process, the water is heated. Before it’s reintroduced into the lake, any excess heat is extracted from the water and used to heat the facility—eliminating the need for natural gas.
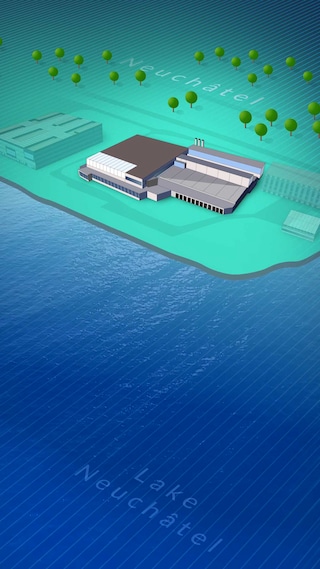
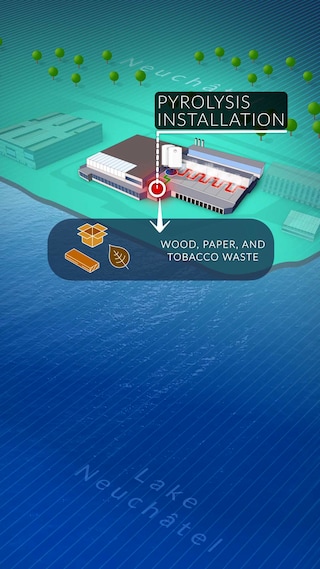
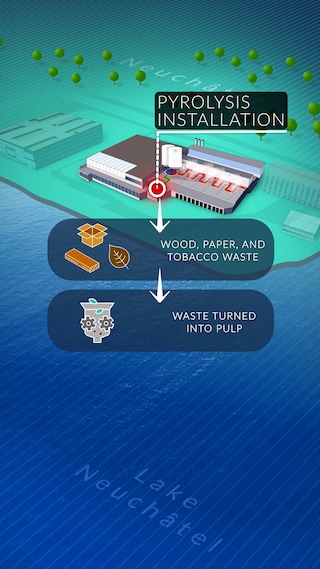
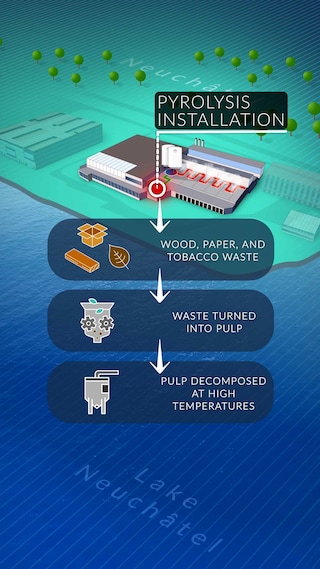
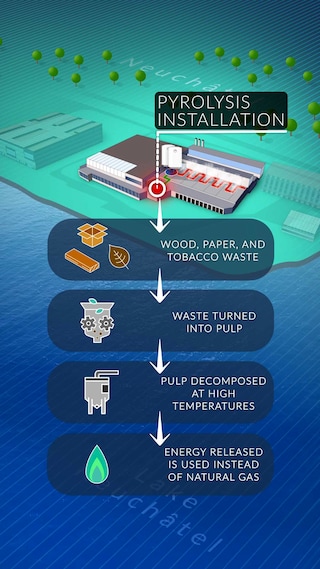
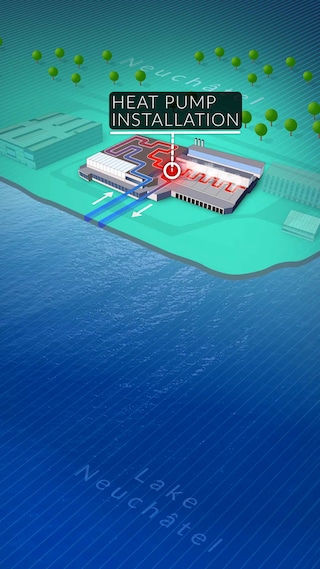
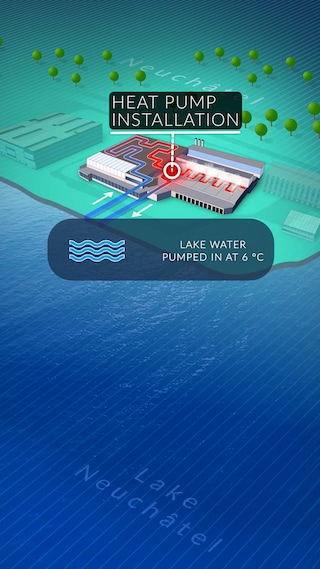
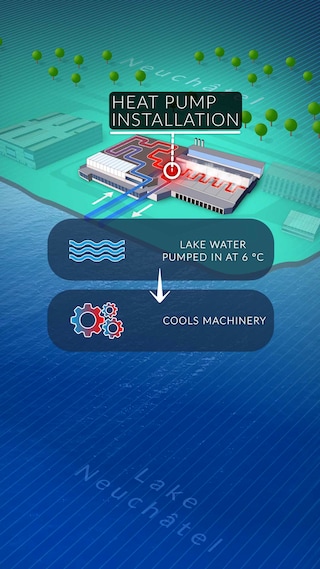
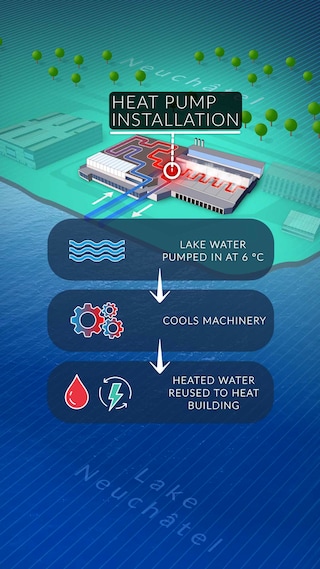
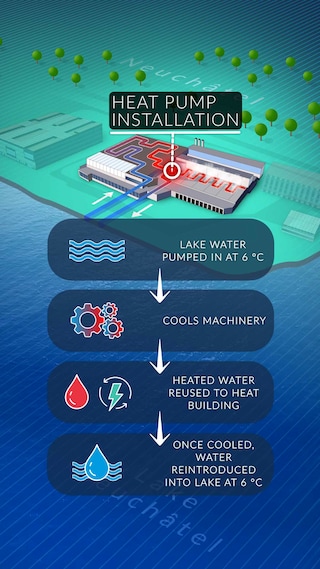
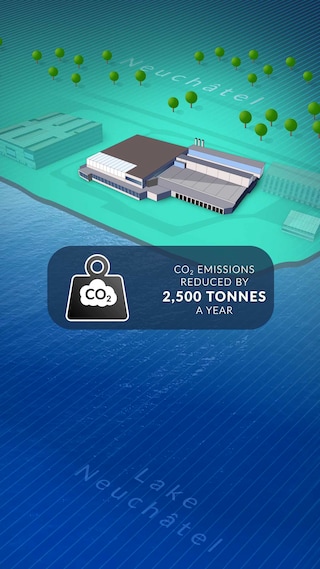
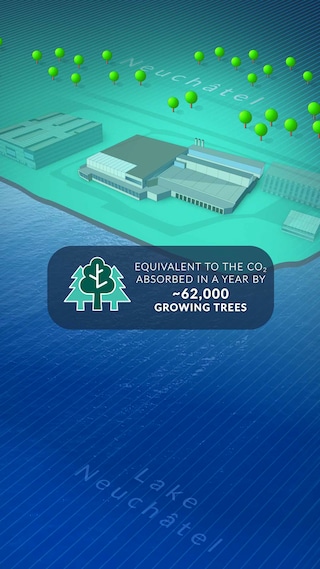
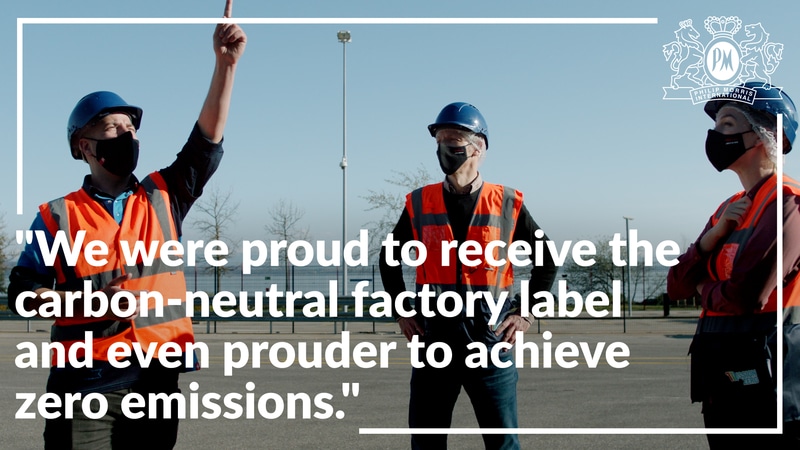
Learn how Frederic Voegele, Manager of Engineering at our facility in Neuchâtel, and his team redesigned PMI’s factory to be carbon neutral.
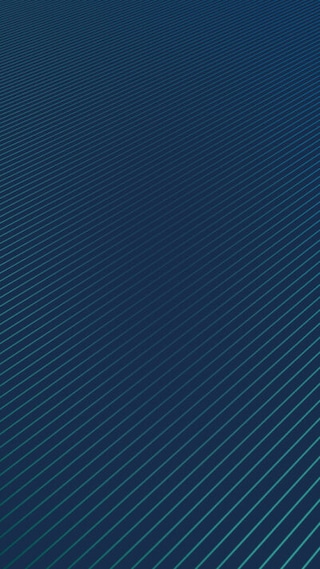
Our progress in cutting CO2 emissions at the Neuchâtel factory
In 2021, the Neuchâtel factory celebrated receiving the Myclimate carbon-neutral factory label for using
sustainable resources and green energy to regulate the temperature of its machinery and buildings.
In 11 years, it has drastically cut its CO2 emissions.
Our progress in cutting CO2 emissions at the Neuchâtel factory
In 2021, the Neuchâtel factory celebrated receiving the Myclimate carbon-neutral factory label for using
sustainable resources and green energy to regulate the temperature of its machinery and buildings.
In 11 years, it has drastically cut its CO2 emissions.